Ammann’s new pivot-steer roller carries on its tradition of manoeuvrability while adding unparalleled visibility and fingertip operator control. In addition, the Ammann ARP 75 Pivot-Steer Tandem Roller also offers adjustable compaction width due to crab mode, a variable range of frequencies – and plenty of compaction punch. The machine is also available in a “combi” version, with four tyres to increase machine usage on more applications and jobsites.
Applications
Depending on the unique steering settings, such as off-set (crab) mode, the machine is well-suited for open, straight jobsites – such as municipal roads or highways – where high productivity is needed. The roller’s manoeuvrability makes it suitable for jobsites such as roundabouts and urban areas where steering accuracy is a priority. High versatility is key to this machine, which makes it an excellent fit for rental fleets and roadbuilding companies.
Innovative cab design
A new symmetrical cab with 360º visibility from the operator station establishes a new market standard. The cab integrates four ROPS posts directly in the main structure and near the doors, not in the cab corners. The new location improves visibility and safety.
The cab is spacious and extremely quiet. It is suspended and isolated from external heat and vibration from the operator station. Those features keep operators comfortable, fresh and focused.
The overall design changes make the machine more compact. Well-designed and positioned water tanks add to the impressive appearance while improving sight lines to all drum surfaces and edges. Operators have an exceptional view around the machine, improving productivity and safety.
The ARP 75 operator station extends beyond the 1×1 meter rule (in both directions) – another significant safety feature.
Fingertip steering
The advanced operator station has integrated, centralised controls that are located near the operator and always easy to reach, regardless of the seat position. This innovative approach reduces necessary reaction times and improves safety.
The operator’s seat is fully adjustable, with a 270° rotation to optimise visibility from the cab. The machine is equipped with Fingertip Steering (FTS), making it more operator-friendly and comfortable. The FTS replaces the traditional steering wheel and allows operators to keep both hands on the armrests for improved comfort. It also offers advanced palm support that prevents repetitive motion fatigue and injuries.
A new 10-inch touch screen helps operators control all machine functions simply, safely and quickly. This includes vibratory parameters, lights, and ACEforce – the advanced Continuous Compaction Control system.
In addition to machine functions, the display provides an overview of fluid levels, indicators and machine status and warnings. The display is installed on an adjustable support, located in front of the operator, and moves with the seat for easy viewing. All these features – a symmetrical cab, unique operating station and rotating seat – are essential to using the machine in forward and reverse without limits.
Built for high productivity
The standard operating width of the ARP 75 is 1500 mm (59,1 in.). To improve machine versatility, “crab mode” (off-set mode) is available. It increases working width and enables compaction close to curbs and obstacles.
Machine working width can be increased slightly to enable compaction around obstacles – or it can be expanded up to 1220 mm (48 in) to total machine working width of 2720 mm (107 in). This significantly improves machine productivity on long, straight jobsites.
Vibratory system development is driven by Ammann’s expertise and produced in-house, improving quality and durability. Standard is a two-stage vibratory system with a multiple range of frequencies that helps operators precisely adjust compaction output. The ARP 75 has adjustable frequencies ranging from 38-55 Hz. It is able deliver compaction output in the range of 47-92 kN per drum.
Steering is precise thanks to a combination of FTS and four steering cylinders – two for each drum. High manoeuvrability results from wide drum turning angles ±24°. This provides an exceptional inner radius of less than 3 meters (9,8 ft.). Varied steering modes are available – front drum only, rear drum only, synchro (where both drums steer) and crab.
The standard machine is equipped with two large water tanks that provide capacity of 900 liters (238 gallons) for drum surface spraying. Highly effective spraying bars, with two high pressure water pumps as standard, boost sprinkling system productivity and efficiency.
Powerful engine
The roller is available mainly for countries with strict emissions regulations and fulfills U.S. EPA Tier 4f and EU Stage V standards. The machines are equipped with Kubota V3307-CR-T diesel engines with power output of 54,4 kW (74 hp) and after-treatment technology EGR+DOC+DPF.
The machine need only be fueled once every two shifts because of a large tank, with a capacity of 180 liters (47,5 gallons).
Intelligent Compaction systems
Available on the ARP 75 are ACEpro or ACEforce Intelligent Compaction systems, which make it easy for operators to monitor and assess compaction progress.
The ACEforce system offered on heavy compaction machines uses absolute measurement (kB value in MN/m) of compaction results, making it easy to correlate with laboratory tests.
ACEpro is an automated measurement and regulation system for controlling and adjusting compaction parameters of Ammann´s rollers. Parameter adjustment is based on continuous measurement of compacted material. Core parameters – such as amplitude and frequency – utilise automatic, stepless regulation.
Both Ammann intelligent compaction systems are compatible with all major GPS manufacturer´s products to provide mapping and operator guidance.
Serviceability
Serviceability, reduced downtime and total cost of ownership are essential to profitability. Machine data is collected from all regions and is reflected in innovative machine development as well as the ECOdrop philosophy.
ECOdrop is a technical solution that makes the machines mostly maintenance free – and more environmentally friendly.
Maintenance is faster and more convenient thanks to a highly accessible engine compartment with a robust design that protects all major components. All maintenance and service points are accessible from the ground. Machines are equipped with external draining points for all operational fluids such as engine oil, hydraulic oil and coolant.
All rollers are equipped with an auto-diagnostics system that communicates with service technicians via machine display. External testing ports on hydraulic components enable quick diagnosis and reduce machine downtime.
Options
A wide range of options can make the compactor more productive, comfortable and serviceable.
Each machine is ready for installation of Ammann’s telematics system, ServiceLink, which monitors the roller’s position, helps with its control and communicates important jobsite data. All this information can be viewed via a portal or mobile app.
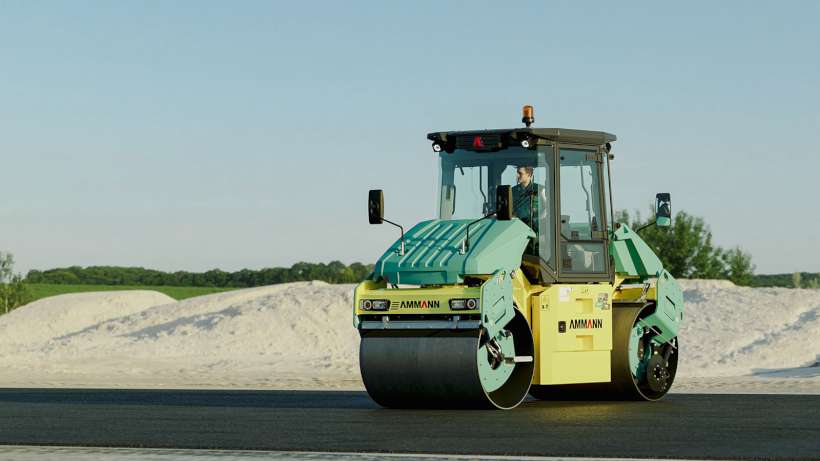