The new H8-18XD series of Hyster Big Trucks features Stage V engines and delivers low running costs in terms of fuel and AdBlue® consumption, with no compromise on performance or durability. “We are constantly evolving our range of Hyster solutions, according to technological developments, changes in legislation, and above all, our customers’ needs,” says Jan-Willem van den Brand, Direct Global Market Development Big Trucks. “Customers can expect high uptime and low TCO (Total Cost of Ownership) in demanding applications where cost pressures are having a big impact.”
Tyre repair and replacement is in fact the second largest cost for most materials handling operations. For this reason, the Hyster trucks feature an adjustable maximum steering angle. This decreases friction when the operator selects the reduced angle, resulting in reduced tyre wear and cost.
“A key way to increase productivity and maximise the profitability of an operation is to prevent downtime for service and maintenance,” says Jan-Willem. “Therefore, improved serviceability is built into the design of all models in the series.”
The service intervals on the new Stage V engine have increased from 500 hours to 1000 hours. In accordance with regulations, the new Hyster trucks use a combination of a Selective Catalytic Reduction (SCR), a Diesel Exhaust Fluid (DEF) like AdBlue® and a Diesel Particulate Filter (DPF). For easy access, both after-treatment units are packed in one box and conveniently positioned on the outside of the truck.
To speed up general maintenance and minimise downtime, the truck series is designed with easy service access, with a display providing key truck performance data and on-board diagnostics on one clear screen.
The Hyster® H8-18XD truck series is available with a variety of wheelbase sizes. Businesses can specify a truck for optimal manoeuvrability in tight spaces, boosting productivity and reducing tyre wear. Where space isn’t an issue, applications can select a model with a larger outer turning radius and lower truck weight to help reduce fuel consumption and costs.
Different truck configurations are available, as well as special engineering options, to accommodate other application-specific requirements, from a reversing fan to improve cooling in dusty paper or construction operations, or different handling attachments to accommodate the load variation encountered in the wood industry.
The truck series also features a redesigned front end and operator-friendly XD cabin, for which the Hyster® H16XD-6 lift truck received a 2020 GOOD DESIGN Award*.
“The cab and front-end design focuses on visibility, ergonomics and comfort to help drive operator productivity throughout an entire shift,” says Jan-Willem. “Not only is a comfortable operator often more productive, but comfort also keeps them happy. This is more important than ever as many markets are encountering a shortage of skills in this area.”
The quiet and comfortable cab has the largest cabin entry area in the industry making it easy to get on and off, and it is spacious enough to wear a hard hat inside.
The cab’s redesigned mast and carriage creates a wider view for the operator, providing greater visibility of fork tips at ground level and trailer height. Operators of the new Hyster® H8-18XD range benefit from an improved sense of stability thanks to the new cast counterweight. This has shifted the trucks’ centre of gravity downwards and towards the rear, minimising bounce.
“Precision handling of fragile, heavy loads in tight spaces is required throughout applications, such as the chemicals, metals and construction industries. These trucks are sometimes required to work closely alongside materials and workers,” says Jan-Willem. “In these operations, a truck needs to deliver powerful performance, but with accuracy, for maximum productivity and less costly damage to loads.”
“With our new series of 8-18 tonne lift trucks, we have simplified the range, while simultaneously offering more choice to customers in their specific application requirements,” adds Jan-Willem.
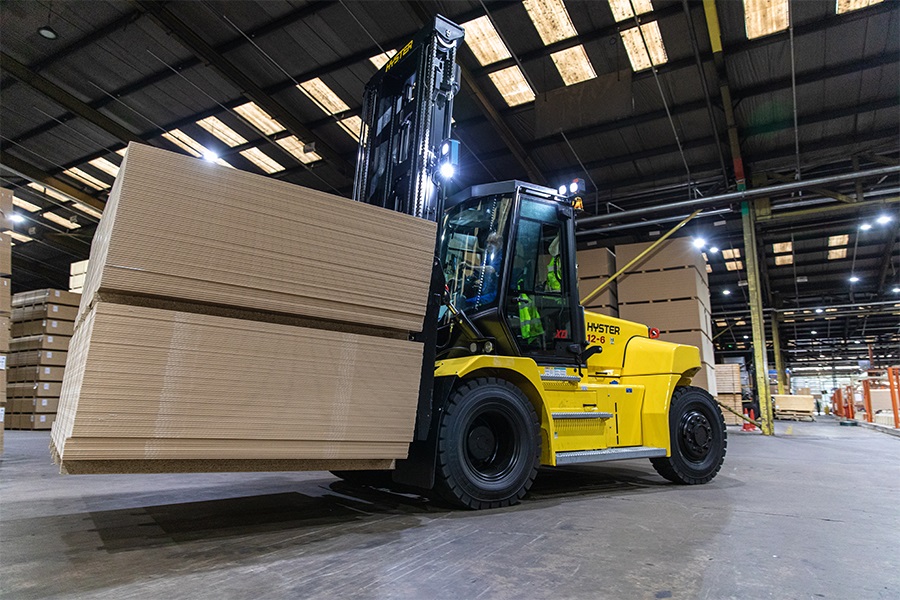